摘要:简述了双组分水性环氧树脂涂料的特点及其用途,分别介绍了水性环氧树脂乳液和水性环氧固化剂的制备方法、双组分水性环氧树脂涂料的分类、混合体系的固化成膜机理和适用期的判断。最后给出了对水性环氧树脂涂料进行配方设计时应考虑的因素。 关键词:水性环氧树脂乳液、水性环氧固化剂、成膜机理、适用期、配方设计 Two-Component Waterborne Epoxy Resin Coating Shi Xuezhen (Shanghai Greenguard Co. Ltd, Shanghai 200082, China) Abstract: This paper briefly introduced the features and applications of two-component waterborne epoxy resin coating. Then the preparations of water-based epoxy resin emulsion and waterborne epoxy hardener, the classification of two-component waterborne epoxy resin coating, the curing and film formation mechanism of the mixed system and the determination of pot life are reviewed. Moreover, the key factors in the design of waterborne epoxy resin coatings' formulation are also indicated. Key word: epoxy resin emulsion, waterborne epoxy hardener, film formation mechanism, pot life, formulation design 1 概况 水性环氧树脂是指环氧树脂以微粒或液滴的形式分散在以水为连续相的分散介质中而配得的稳定分散体系[1,2]。由于环氧树脂是线型结构的热固性树脂,所以施工前必须加入水性环氧固化剂,在室温环境下发生化学交联反应,环氧树脂固化后就改变了原来可溶可熔的性质而变成不溶不熔的空间网状结构,显示出优异的性能。水性环氧树脂涂料除了具有溶剂型环氧树脂涂料的诸多优点,如对众多底材具有极高的附着力,固化后的涂膜耐腐蚀性和耐化学药品性能优异,并且涂膜收缩小、硬度高、耐磨性好、电气绝缘性能优异等,还具有不含有机溶剂或挥发性有机化合物含量较低,不会造成空气污染,因而满足当前环境保护的要求;同时以水作为分散介质,价格低廉、无气味、不燃,储存、运输和使用过程中的安全性也大为提高;再次是水性环氧树脂涂料的操作性能好,施工工具可用水直接清洗。水性环氧树脂涂料的突出优势还表现在该混合体系可在室温和潮湿的环境中固化,有合理的固化时间,并保证有很高的交联密度,这是通常的水性丙烯酸涂料和水性聚氨酯涂料所无法比拟的。 通过对环氧树脂基材、固化剂以及各种改性剂和助剂的合理选择,就可制备出性能各异的水性环氧树脂涂料。水性环氧树脂涂料的诸多性能特点决定了其与溶剂型或无溶剂型环氧树脂涂料相比具有更为广泛的应用前景。目前水性环氧树脂涂料的应用主要包括下面几个方面:⑴、在工业地坪涂装方面,可作为高性能环境适应型地坪涂料替代溶剂型环氧树脂涂料,也可作为聚合物成分掺入水泥砂浆制成高性能聚合物砂浆地坪材料[3];⑵、配成清漆可用于木质地板,替代目前市场上广泛使用的溶剂型聚氨酯水晶地板漆,配成色漆可替代溶剂型环氧树脂和聚氨酯磁漆,用于厨房、家具和机械设备等[1];⑶、借助于水性环氧树脂涂料优良的机械性能和与水泥良好的配伍性制备高强混凝土,其中水性环氧树脂涂料作为辅助成分加到混凝土或水泥砂浆中,并可提高混凝土的抗渗性;⑷、利用环氧树脂对水泥材料和众多有机材料良好的粘接性能以及环氧树脂本身优异的机械性能和耐化学药品性能作为混凝土粘接剂和防水堵漏材料;⑸、利用环氧树脂优异的耐腐蚀性作为防腐蚀涂料,用作钢铁和船舶的防腐底漆[4-6];⑹、与其它通用乳液(如聚丙烯酸乳液、水性聚氨酯)配合使用,起协同效应得到具有不同性能的涂层。 2 水性环氧树脂乳液的制备方法 环氧树脂本身不溶于水,不能直接加水进行乳化,要制备稳定的水性环氧树脂乳液,必须设法在其分子链中引入强亲水链段或者在体系中加入亲水亲油组分。根据制备方法的不同,环氧树脂水性化有以下三种方法:机械法、化学改性法和相反转法。 2.1 机械法 将固体环氧树脂预先磨成微米级的环氧树脂粉末,在加热的条件下加入乳化剂水溶液,通过激烈的机械搅拌即可制得水性环氧树脂乳液[7]。用机械法制备水性环氧树脂乳液的优点是工艺简单,所需乳化剂用量较少,但乳液中环氧树脂分散相微粒尺寸较大,约为50μm 左右,粒子形状不规则且尺寸分布较宽,所配得的乳液稳定性差,粒子之间容易相互碰撞而发生凝结现象,并且该乳液的成膜性能也欠佳。当然提高搅拌分散时的温度可以促进乳化剂分子在环氧树脂微粒表面更为有效地吸附,使得环氧树脂微粒能较为稳定地分散在水相中。 2.2 化学改性法 化学改性法是通过对环氧树脂分子进行改性,将离子基团或极性基团引入到环氧树脂分子的非极性链上,使它成为亲水亲油的两亲性聚合物,从而具有表面活性剂的作用,这类改性后的高聚物又称离聚体(ionomer)[2,8]。当这种改性聚合物加水进行乳化时,疏水性高聚物分子链就会聚集成微粒,离子基团或极性基团分布在这些微粒的表面,由于带有同种电荷而相互排斥,只要满足一定的动力学条件,就可形成稳定的水性环氧树脂乳液。用化学改性的方法制备的水性环氧树脂乳液中分散相粒子的尺寸很小,约为几十到几百个纳米,但化学改性法的制备步骤不易控制,产品的成本也较高。根据引入的具有表面活性作用的亲水基团性质的不同,自乳化型水性环氧树脂乳液可分为阴离子型、阳离子型和非离子型三种。 2.2.1 阴离子型 通过适当的方法在环氧树脂分子链中引入羧酸、磺酸等功能性基团,中和成盐后的环氧树脂就具备了水可分散的性质。常用的改性方法有功能性单体扩链法和自由基接枝改性法。功能性单体扩链法[9]是利用环氧基与一些低分子扩链剂如氨基酸、氨基苯甲酸、氨基苯磺酸等化合物上的胺基反应,在环氧树脂分子链中引入羧酸、磺酸基团,中和成盐后就可分散在水相中。自由基接枝改性法[10]是利用双酚A环氧树脂分子链中的亚甲基活性较大,在过氧化物作用下易于形成自由基,能与乙烯基单体共聚,可将丙烯酸、马来酸酐等单体接枝到环氧树脂分子链中,再中和成盐后就可制得能自乳化的环氧树脂。 2.2.2 阳离子型 含胺基的化合物与环氧树脂反应生成含叔胺或季胺碱的环氧树脂,再加入挥发性有机一元弱酸如醋酸中和得到阳离子型的水性环氧树脂[8]。这类改性后的环氧树脂在实际中应用较少,这是因为水性环氧固化剂通常是含有胺基的碱性化合物,两个组分混合后,体系容易出现破乳和分层现象而影响该体系的使用性能。 2.2.3 非离子型 通过含亲水性的聚氧乙烯链段的羟基或胺基与环氧树脂分子中的环氧基反应,将聚氧乙烯链段引入到环氧树脂分子链中,得到含非离子亲水链段的水性环氧树脂,该改性的环氧树脂分散在水相中形成的体系具有很好的稳定性,分散相粒子的平均粒径小于1um,并且该分散体系与水性环氧固化剂混合后的适用期也有所延长[1]。同时在引入聚氧乙烯链段后,交联固化后的网链分子量有所提高,交联密度下降,形成的涂膜有一定的增韧作用。 2.3 相反转法 相反转是一种制备高分子树脂乳液较为有效的方法[7,11],几乎可将所有的高分子树脂借助于外乳化剂的作用并通过物理乳化的方法制得相应的乳液。相反转[12]原指多组分体系(如油/水/乳化剂)中的连续相在一定条件下相互转化的过程,如在油/水/乳化剂体系中,其连续相由水相向油相(或从油相向水相)的转变,在连续相转变区,体系的界面张力最低,因而分散相的尺寸最小。用相反转法制备水性环氧树脂乳液的具体过程是在高速剪切作用下先将外乳化剂和环氧树脂混合均匀,随后在一定的剪切条件下缓慢地向体系中加入蒸馏水,随着加水量地增加,整个体系逐步由油包水向水包油转变,形成均匀稳定的水可稀释体系。在这过程中,水性环氧树脂乳液的许多性质会发生突变,如体系的粘度、导电性和表面张力等,通过测定体系乳化过程中的电导率和粘度的变化[13,14]就可判断相反转是否完全。该乳化过程可在室温环境下进行,对于固体环氧树脂,则需要借助于少量有机溶剂或进行加热来降低环氧树脂本体的粘度,然后再进行乳化。 3 水性环氧固化剂 水性环氧树脂涂料一般用在室温固化的场合[1]。多乙烯多胺,如二乙烯三胺、三乙烯四胺及间苯二胺是常用的溶剂型环氧树脂固化剂,但它们一般溶于水,在气温较低或空气湿度较大时会由于该类固化剂吸收空气中的水分、二氧化碳而使得涂膜泛白,附着力下降。而且多乙烯多胺本身容易挥发,并有刺激性气味,与环氧树脂的相容性也较差,成膜后会有部分多乙烯多胺在涂膜表面析出而造成缺陷。实际使用的水性环氧固化剂大多为它们的改性产物,包括酰胺化多胺[5]、聚酰胺[15]和环氧-多胺加成物,通过在多乙烯多胺分子中引入非极性基团,改善了它们与环氧树脂的相容性。早期酰胺化多胺用作水性环氧树脂涂料的固化剂,由于酰胺化的多胺具有乳化剂的功能,因而低分子量的液体环氧树脂不需要预先乳化,而由酰胺化的多胺在施工前混合乳化,具有施工性能好、适用期长等优点,但固化后涂膜的性能不佳,耐水性和耐化学药品性能差。 由于酰胺化的多胺和聚酰胺类固化剂的缺点,改性后涂膜的性能又没有明显的提高,因此目前研究的水性环氧固化剂主要指环氧-多胺类加成物。通过对多乙烯多胺进行改性,使其成为性能良好的水性环氧固化剂,保证固化后的涂膜性能接近溶剂型环氧树脂涂料,具体的改性方法如下: ⑴、提高它与环氧树脂的相容性,这有利于分散后环氧树脂乳液的稳定性并可避免固化后由于固化剂析出而造成的表面缺陷。提高相容性的途径是与单环氧化合物或多环氧化合物反应。典型的芳香族单环氧化合物为苯基或甲苯基环氧丙基醚,典型的脂肪族单环氧化合物为丁基环氧丙基醚,典型的芳香族多环氧化合物为双酚A型环氧树脂、双酚F型环氧树脂和酚醛环氧树脂。 ⑵、如果是由水性环氧固化剂在施工前对液体环氧树脂进行混合乳化,这类固化剂必须既是交联剂又是乳化剂,因而改性后的多胺-环氧加成物应有表面活性剂的作用,具体的改性途径是在多胺-环氧加成物的分子链中引入具有表面活性作用的分子链段,这部分链段在体系中起内乳化剂的作用[16,17]。 ⑶、延长水性环氧树脂涂料的适用期。要延长水性环氧树脂涂料的适用期,通常有必要降低水性环氧固化剂的活性。多乙烯多胺分子中包括伯胺氢和仲胺氢,而伯胺氢的活性要比仲胺氢高得多,通过封端剂将伯胺氢反应掉是降低多胺-环氧固化剂活性的有效途径。封端剂一般为单环氧化合物,如丁基环氧丙基醚、苯基环氧丙基醚和甲苯基环氧丙基醚。但从相容性角度考虑,采用脂肪族单环氧化合物和芳香族单环氧化合物配合使用更为合适。 ⑷、保持良好的水可分散性。多乙烯多胺是水溶性的,但与环氧树脂加成后,其亲水性有所下降,因此合成时必须考虑亲水亲油平衡,使其改性后的多胺-环氧固化剂仍有良好的水可分散性。一般采用成盐的方法,一方面中和一部分伯胺氢,另一方面又可适当地提高其亲水性。通常选用有机挥发性一元弱酸(如醋酸),它在固化后基本挥发掉,不会影响涂膜的耐腐蚀性和耐化学药品性。 4 水性环氧树脂涂料的分类 室温固化的水性环氧树脂涂料体系一般分为下面4类: ⑴、Ⅰ型水性环氧树脂体系,由低分子量的液体环氧树脂(环氧当量在190左右)和水性环氧固化剂组成[1,16,17]。这类体系中的环氧树脂一般预先不乳化,而由水性环氧固化剂在使用前混合乳化,因而这类固化剂必须既是交联剂又是乳化剂。水性环氧固化剂合成时是以多乙烯多胺为基础,通过在其分子中引入具有表面活性作用的分子链段,使其成为两亲性分子,能够很好地分散或溶解在水中,从而对低分子量的液体环氧树脂具有良好的乳化作用。Ⅰ型水性环氧树脂体系的优点是可配成零VOC(Volatile organic compound) 和NHAP(Non-hazardous air pollutant)的涂料,涂膜硬度增长较快。其缺点是采用的树脂是低分子量的液体环氧树脂,在水分蒸发后仍需要经过一定的反应时间才能达到表干;体系的粘度随搁置时间的延长而快速增加,表现为适用期短,约为2~4小时;并且在适用期范围内体系流变性能也不稳定。 ⑵、Ⅱ型水性环氧树脂体系,由高分子量的固体环氧树脂乳液和水性环氧固化剂组成[18]。环氧树脂是亲油性分子,其亲水亲油平衡值(HLB)小于3,要得到稳定的水性环氧树脂乳液,应在其分子中引入具有表面活性作用的亲水链段,如聚氧乙烯聚氧丙烯链段,同时在引入这种链段后,交联形成的网链分子量有所提高,交联密度下降,所以对涂膜有一定的增韧作用。实际上使用的大多数高分子量固体环氧树脂乳液都是以低分子量的液体环氧树脂为原料,采用含聚氧乙烯聚氧丙烯链段的环氧丙基醚通过双酚A扩链和低分子量环氧树脂反应,将聚氧乙烯聚氧丙烯链段引入到环氧树脂分子链中,该产物用水和乙二醇醚类稀释就可得到稳定的水性环氧树脂乳液[19]。由于Ⅱ型水性环氧树脂体系中的环氧树脂已预先配成乳液,不需要水性环氧固化剂再对环氧树脂进行乳化,因而只需具有交联剂的功能。水性环氧树脂体系的固化反应是水性环氧固化剂分子中的胺基与环氧树脂分子中的环氧基反应,而高分子量环氧树脂的反应活性较低分子量环氧树脂小,因此Ⅱ型水性环氧树脂体系的适用期较Ⅰ型的长,但同时也造成涂膜的硬度增加缓慢。加入少量成膜助剂可改善Ⅱ型水性环氧树脂体系的成膜性能,Ⅱ型水性环氧树脂体系涂膜后,一旦水分蒸发,即使环氧树脂还未交联固化也已成固体状态,达到表干的要求,因而Ⅱ型水性环氧树脂体系的表干时间较Ⅰ型的短[20]。 ⑶、Ⅲ型水性环氧树脂体系,由低分子量的液体环氧树脂乳液和水性环氧固化剂组成,低分子量液体环氧树脂乳液一般采用相反转技术制备。为了克服外加低分子量表面活性剂乳化环氧树脂的缺点,开发出新型的反应性环氧树脂乳化剂。通过将具有表面活性作用的分子链段结合到环氧树脂分子链中,这样该乳化剂分子中既含有表面活性作用的链段(亲水链段),又含有环氧树脂链段(亲油链段),大大改善了乳化剂与环氧树脂的相容性。然后用该乳化剂并借助于相反转技术就可配制分散相平均粒径为约1~2μm的低分子量液体环氧树脂乳液。同时该反应性乳化剂分子末端还含有环氧基,可与水性环氧固化剂分子中的胺基反应,成膜后乳化剂分子不会从固化体系中析出,并对涂膜有一定的增韧作用。 ⑷、Ⅳ型水性环氧树脂体系,由水性环氧树脂乳液和聚氨酯改性环氧固化剂组成。环氧树脂涂料具有附着力高、绝缘性能好、硬度高等优点,但形成的涂膜的柔韧性和耐磨性则不及聚氨酯涂料,因此用适量的聚氨酯改性环氧树脂,可制得综合性能良好的聚氨酯改性环氧固化剂,用它来固化水性环氧树脂乳液可以改善水性环氧树脂涂料的性能。聚氨酯改性环氧固化剂的具体合成路线为聚氨酯首先和聚醚多元醇反应,在聚氨酯分子链中引入亲水基团,制得聚氨酯预聚物,再将此预聚物与环氧树脂进行接枝反应,反应结束后加入三乙胺中和成盐,同时在水相中进行扩链和分散。 5 水性环氧树脂体系的固化成膜机理 水性环氧树脂涂料是一种乳液涂料[1],其成膜机理与一般的聚合物乳液涂料如丙烯酸乳液的成膜有很大的区别,同时与溶剂型环氧树脂涂料的成膜也不完全相同。一般聚合物乳液涂料的固化成膜为一物理过程,分散相粒子的玻璃化温度较低,在水分挥发后就形成紧密堆积的结构,并在毛细管压力作用下凝结成膜。在溶剂型环氧树脂涂料体系中,环氧树脂和固化剂均以分子形式溶解在有机溶剂中,形成的体系是均相的,固化反应在分子之间进行,因而固化反应进行得比较完全,所形成的涂膜也是均相的[16-17]。 水性环氧树脂涂料为多相体系,环氧树脂以分散相形式分散在水相中,水性环氧固化剂则溶解在水中。图1为水性环氧树脂涂料的固化成膜示意图[18],将两个组分混合后的体系涂布在基材上,在比较适宜的温度条件下,水分蒸发得很快。当大部分水分蒸发后,环氧树脂乳胶粒子相互接触,形成紧密堆积的结构,残余的水分和固化剂分子则处在环氧树脂分散相粒子的间隙处。随着水分的进一步蒸发,环氧树脂分散相粒子开始凝结,形成更为紧密的六边形排列结构。与此同时,固化剂分子扩散到环氧树脂分散相粒子的界面及其内部发生固化反应。该固化成膜机理也可解释为水性环氧树脂体系由水包油的状态向油包水转变,与用相反转法配制环氧树脂乳液的过程刚好相反[21]。 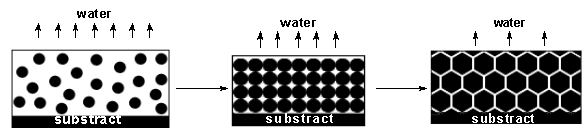 ● 乳胶粒子 水分蒸发,乳胶粒子相互靠近, 水分进一步蒸发 □ 水 +固化剂 形成紧密堆积, 凝结形成六边形结构 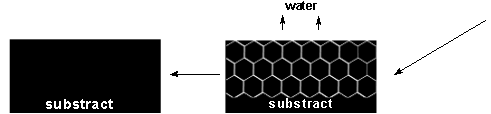 形成均相、固化完全的涂膜 进一步凝结,乳胶粒子和固化剂开始反应 图1 水性环氧树脂涂料的固化成膜过程示意图 假定用相反转法配制的水性环氧树脂乳液中分散相粒子的平均粒径为0.5μm,又设其密度为1.16g/mL,环氧树脂分子量为1000,并不考虑在水中的溶胀,则可计算出每个环氧树脂乳胶粒中含有4.6×107个分子,所以水性环氧树脂体系的固化是由固化剂向环氧树脂分散相粒子的扩散速度所决定的,这与溶剂型环氧树脂体系相比其固化成膜过程更为复杂[20]。固化剂分子首先和环氧树脂分散相粒子的表面接触发生固化反应,随着固化反应的进行,环氧树脂分散相的分子量和玻璃化温度逐渐提高,使得固化剂分子向环氧树脂分散相粒子内部的扩散速度逐渐变慢,这就意味着环氧树脂分散相粒子内部进行的固化反应较其表面的少,内部交联密度也较低。同时随着固化反应的进行,环氧树脂分散相粒子逐渐变硬,粒子之间也很难相互作用而凝结成膜。因而水性环氧树脂涂料同溶剂型环氧树脂涂料相比,很难形成均相、完全固化的涂膜。因此,对于水性环氧树脂涂料,其固化是否充分主要取决于以下两个因素: (1)、环氧树脂分散相粒子的粒径。在保证水性环氧固化剂用量相同的情况下,环氧树脂分散相粒子的粒径较小时,粒子表面的固化剂浓度较为适中,表面固化速度较慢,固化剂分子有足够的时间扩散到整个环氧树脂分散相粒子,使之固化完全,因而可以形成均匀、完全固化的涂膜。反之,分散相粒子尺寸较大时,粒子表面的固化剂浓度相对较高,导致表面快速固化;随着固化反应的进行,环氧树脂分散相粒子的表观粘度不断增大,其玻璃化温度也会逐渐提高,使得固化剂分子向环氧树脂粒子内部扩散速度逐渐变慢,环氧树脂粒子内部来不及固化而致使涂膜固化不完全。 (2)、环氧固化剂与环氧树脂的相容性。提高环氧固化剂与环氧树脂的相容性,有利于水性环氧树脂乳液分散后体系的稳定性,并且两者的相容性越好,环氧固化剂越容易向环氧树脂微粒内部扩散,有利于固化反应的进行。 6 适用期 双组分反应性涂料都有一个适用期的问题。由于水性环氧树脂体系与溶剂型环氧树脂体系的固化成膜机理有所不同,因而适用期的判断准则也不完全相同[16,18]。对溶剂型环氧树脂体系,体系的粘度随搁置时间的延长而不断增大,故该体系的适用期可用粘度随时间的变化来表示,即从两个组分混合至体系粘度增大到无法施工的时间。但对水性环氧树脂体系,则不能用体系粘度随时间的变化来判定。环氧树脂乳液以及相应配得的清漆都会显示出触变性和假塑性,属于典型的水分散体系。水性环氧树脂涂料的两个组分混合后体系粘度变化比较复杂,有的体系的粘度随搁置时间的延长逐步增加,而有的体系粘度在两个组分混合后迅速下降,并在较长时间内基本保持不变。 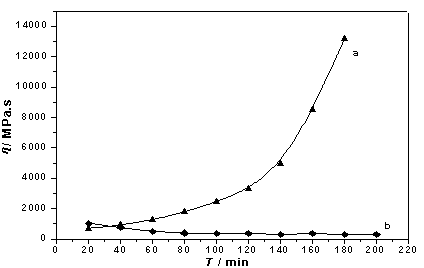 图2 水性环氧树脂涂料体系粘度随搁置时间的变化 如图2所示,两个体系采用相同的乳液和不同的固化剂,研究发现曲线a的粘度随着搁置时间的延长而逐步提高,是I型水性环氧树脂体系,而曲线b所代表的体系则属于II型水性环氧树脂体系。对于II型水性环氧树脂体系粘度呈下降趋势的现象可作以下的分析:因为II型水性环氧树脂体系所用的环氧-多胺固化剂是水溶性的,当两个组分混合后,环氧树脂以微粒形式分散在环氧固化剂水溶液中,该体系的粘度主要由水相的粘度决定。随着搁置时间的延长,水性环氧固化剂分子从水相不断向环氧树脂微粒表面及其内部扩散,致使水相中的固化剂浓度不断下降,宏观上就表现为体系的粘度不断降低[20]。当环氧树脂微粒表面的表观粘度增大到一定程度时,固化剂分子向其内部的扩散速度有所减慢,体系的粘度也就基本保持不变。因此,用体系粘度随搁置时间的变化来确定水性环氧树脂体系的适用期是不可靠的,而应选择别的特征参数,如涂膜光泽度、玻璃化温度[21]等等。 7 水性环氧树脂涂料的配方设计 通过对环氧树脂、水性环氧固化剂、颜填料以及各种助剂的选择,可制备性能不同的水性环氧树脂涂料[1]。因而在设计水性环氧树脂涂料的配方时需考虑以下因素: ⑴、环氧树脂与水性环氧固化剂的当量比[20]。环氧树脂与水性环氧固化剂的当量比因水性环氧树脂涂料的类型不同而有较大差异,对于Ⅰ型水性环氧树脂体系,由于是用水性环氧固化剂直接乳化低分子量的液体环氧树脂,体系中具有表面活性作用的链段较高,适当提高两者的当量比,可降明显改善涂膜的耐水性和硬度,一般控制在比理论值高5~10%的范围内[16,17]。对其它类型的水性环氧树脂体系,若适当增加环氧树脂的用量,有助于提高涂膜的耐水性和耐腐蚀性,这是因为环氧树脂是亲油的,而水性环氧固化剂的亲水性较强,适量减少水性环氧固化剂就可提高该体系的亲油性。在某些情况下,若采用环氧固化剂过量,则有助于提高涂膜的固化速度和交联密度,从而有利于提高涂膜的耐溶剂性、耐污染性、附着力、干燥速度等,关于这一点可根据具体应用场合而加以调整。 ⑵、颜填料。根据水性环氧树脂涂料的应用要求来选择恰当的颜填料[22]。对耐酸碱介质的场合,可采用氧化铁红和沉淀硫酸钡等颜填料;对于有耐光和耐热要求的场合,可采用氧化锌和云母氧化铁等颜填料;若要增加涂膜的耐化学药品性和提高其机械性能,则应选择云母和滑石粉类的填料。当然,考虑到水性环氧固化剂呈弱碱性,应避免采用酸性的颜填料,避免两组分混合后出现破乳和分层情况。水性环氧树脂涂料是双组分涂料,颜填料既可加到环氧树脂乳液组分中,也可以加在水性环氧固化剂组分中,但为了使用方便,应使加入颜填料后的两个组分的当量比较为接近。 ⑶、助剂。助剂是水性环氧树脂涂料生产、储存及施工过程中不可缺少的组分之一,应充分利用各种助剂对涂料以及最终涂膜性能的作用,有针对性地选用各种助剂。水性环氧树脂涂料应选用的助剂有成膜助剂、消泡剂、分散剂、流变调节剂等,具体选择时应考虑与水性环氧树脂体系的相容性,避免出现凝胶和涂膜浮油等缺陷。 参考文献 [1] 陶永忠,陈铤,顾国芳.涂料工业,2001,31(1):36-38. [2] 顾宇昕,黄玉惠,廖兵等.高分子学报,1999,4:477-482. [3] 周天寿,沈志明,王宝根. 新型建筑材料,2001,(5):16-18. [4] Almeida E, Santos D, Oruchurtu J. Prog Org Coat,1999,37(3):131-140. [5] Hawkins CA, Sheppard AC, Wood TG. Prog Org Coat,1997,32(1):253-261. [6] 赵金榜. 涂料工业,2001,31(6):17-19. [7] 杨振忠,许元泽,赵得禄等.高分子通报,1999,3(9):190-194. [8] 刘小平,郑天亮.涂料工业,2000,30(10):33-35. [9] Zhang ZY, Huany YH, Liao B, et al. Eur Polym J,2001,37(6):1207-1211. [10] Pan GR, Wu LM, Zhang ZQ, et al. J Appl Polym Sci ,2002,83 (8): 1736-1743. [11] Yang ZZ, Xu YZ, Zhao DL, et al. Colloid Polym Sci,2000,278(12):1164-1171. [12] 杨振忠,许元泽,赵得禄等.高分子学报,1998,9:78-82. [13] 王进,杜宗良,李瑞霞等.功能高分子,2000,13(2):141-144. [14] Kojima S, Watanabe Y. Polym Eng Sci, 1993, 33(5):253-259. [15] Wegmann A. J Coating Technol, 1993, 65(827):27-34. [16] 陶永忠,陈铤,顾国芳. 建筑材料学报,2000,3(4):349-354. [17] 陶永忠,陈铤,顾国芳. 胶体与聚合物,2000,19(2):19-22. [18] 陈铤,顾国芳. 建筑材料学报,2001,4(4):356-361. [19] Galgoci EC, Komar PC, Elmore JP. J Coating Technol, 1999,71(891):45-72. [20] 顾国芳,陈铤,陶俊等. 化学建材,2001,17(3):16-20. [21] Wegmann A. Prog Org Coat,1997,32(1):231-239. [22] Muller B, Oughourlian C, Traintaficlidis D. J Coating Technol,2001,73(917):81-84.
|